A lathe is a machine that is used to shape wood or metal or other materials by spinning it and using various cutting tools. It is an essential machine in many workshops and factories.
Most people who buy a new lathe only think about the machine itself. But there are a lot of accessories that can make your life much easier – and help you get better results.
So which accessories should you get? It depends on what you want to use the lathe for and what kind of projects you plan on doing. This article will recommend some essential accessories for a new lathe and explain what they are used for.
Chisels Tools
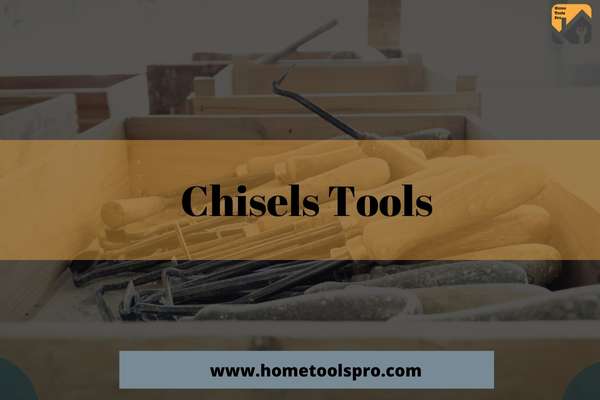
Chisels are one of the most important tools used in lathe machines. They come in different sizes, shapes and designs depending on their intended purpose. In general, chisels are used to remove wood or metal from a workpiece in order to create a desired shape or finish.
There are many different types of chisels available on the market today. Some of the most common include:
Parting Tool:
A parting tool is a type of chisel that is used to create a groove or channel in wood. It is also sometimes used to cut, trim, or shape awkward corners and areas where other tools might not be able to reach.
Parting tools come in various shapes and sizes, depending on the specific application.
The most common type has a straight cutting edge with a rounded end, but there are also variations that have a curved cutting edge or even multiple Cutting edges.
When using a parting tool, applying steady pressure and long strokes are important for the best results. It’s also important not to apply too much pressure, as this can cause the tool to dig into the wood and create an uneven or jagged surface.
Skew Chisel:
A skew chisel with an angled blade is used to create decorative edges on woodworking projects.
The angle of the blade relative to the handle can vary but is typically around 30 degrees. Skew chisels are also often used to hollow out small areas or shape curves.
Most standard woodworking chisels have a bevelled edge on one side and a flat edge on the other. A skew chisel has two bevelled edges (upper and lower), meeting at a sharp point.
Despite its advantages, the skew chisel can be more difficult to use than a standard chisel. This is because the cutting edge is angled, meaning that it can “catch” on the wood if not used correctly.
Finger Nail Gouge:
A fingernail gouge is a type of chisel that is used for carving wood. It has a long, thin blade with a U-shaped profile and a sharp point. This type of chisel is ideal for removing small amounts of wood quickly and easily.
Finger nail gouges are also called V-gouges or U-gouges. They can be used to carve letters and designs into wood or to create decorative details on furniture and other wooden objects.
Bowl Gouge:
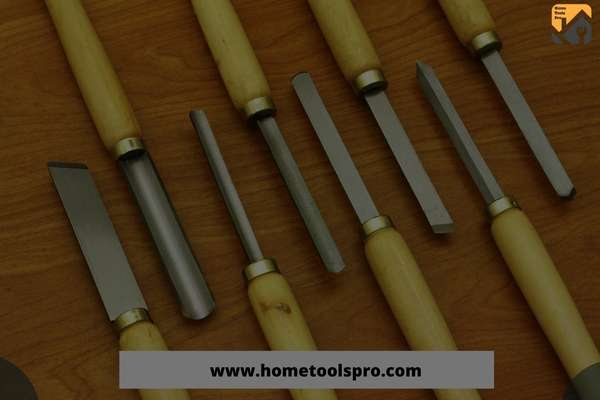
A bowl gouge is a cutting tool that is used to shape the inside of a bowl. The bowl gouge has a long, curved blade with a sharp point at the end.
The blade is held in place by a handle that is attached to the blade with a ferrule. The handle can be made from any material but is typically made from wood or metal.
The blade of the bowl gouge is angled so that it cuts into the wood at an angle of about 45 degrees.
This angle gives the bowl gouge its cutting power and makes it easier to control. When using a bowl gouge, you will need to use both hands; one hand on the handle and one hand on the blade.
Spindle Gouge:
A spindle gouge is a type of chisel designed for detailed work on small, cylindrical surfaces.
It has a U-shaped cross-section with a rounded, spoon-like blade that tapers to a point. The blade can be rotated in the handle to change the angle of attack, making it versatile for creating different shapes and textures.
Spindle gouges are often used for shaping woodturning projects such as bowls, puppets, and other small objects.
They can also be used for detail work on furniture parts like chair legs and table legs carvings and other fine woodworking projects.
A spindle gouge can produce very precise cuts and smooth finishes when sharpened properly.
Roughing Gouge:
A roughing gouge is a type of chisel used to quickly remove large amounts of wood. It has a U-shaped cross-section with a wider and thicker blade than a standard chisel.
The blade of the roughing gouge is also slightly curved, making it more efficient at removing wood than a straight-edged chisel. Roughing gouges are typically used for shaping the outside of a bowl or other rounded object.
They can also be used for quickly removing excess wood from a turning blank or carving project. Roughing gouges are not typically used for detailed work or for finishing cuts.
06 Piece Chisels Tool Set
Centres
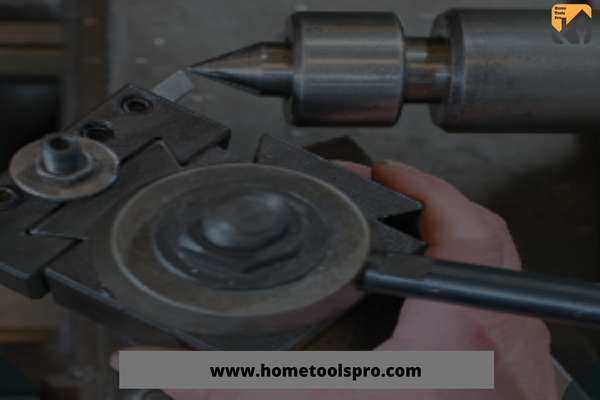
Centres are used in lathes to support long or heavy workpieces. They are also used to position the workpiece for turning accurately.
The centre is a cone-shaped piece of metal with a pointed end and a larger base. The pointed end is inserted into the hole in the workpiece, and the larger base rests on the bed of the lathe. This provides stability and prevents the workpiece from rotating while machined.
Live Type:
A live centre is a type of lathe centre that is used to support the workpiece near its ends.
Unlike a dead centre, which can only be used to turn between centres, a live centre can also turn the workpiece on its outside surface.
This is because the live centre has hardened bearings that allow it to pivot around its point of contact with the workpiece.
Dead Type:
Dead centres are devices used to support the workpiece on a lathe between the live centre and tailstock.
It is also cone-shaped (taper) so that when tension is applied to the workpiece, it will not move axially (in and out) yet still be able to rotate.
The further you get from the centre of rotation, the greater the friction force between the workpiece and the rotating object.
Chucks

Chucks are devices used in lathes to hold a workpiece in place. They come in two main types: the plain and self-centred types.
The plain type is a cylindrical piece of metal or other material with a hole drilled through it. The self-centring type has a tapered hole that allows it to grip the workpiece more securely.
4 Jaw Independent:
The 4 Jaw Independent Chuck” is one of the most common chucks used on lathes. It is an accessory that attaches to the lathe spindle and holds round stock while it is being machined.
The “jaws” of the chuck grip the stock from all sides, keeping it secure while it is being turned. This chuck type is especially useful for machining symmetrical or otherwise irregularly shaped parts.
3 Jaw Universal:
A 3 Jaw Chuck is a device used to secure cylindrical objects for machining.
The chuck has three jaws that close in on the object and grip it tightly.
This type of chuck is called a “universal” chuck because it can be used to hold many different sizes and shapes of objects.
A 3 jaw chuck is the most common type of chuck found on lathes.
Combination:
Combination Chuck is a type of lathe chuck that combines the features of a three-jaw chuck with a four-jaw chuck.
It allows for greater flexibility when machining round parts, as it can grip the part from two opposing sides.
Additionally, it is less likely to damage the part being machined than a four-jaw chuck would be.
Magnetic Chuck:
A magnetic chuck is a type of chuck that uses a series of magnets to hold the workpiece in place.
They are most commonly used on lathes but can also be used on other types of machining centres.
The advantage of a magnetic chuck over other chucks is that they can securely hold very small workpieces without damaging them.
This is because the magnets create a very strong clamping force that will not deform or damage the workpiece.
Adapters
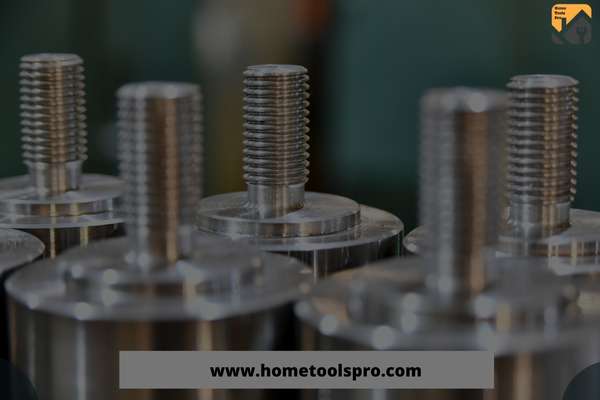
Adapters are devices that are used to connect two pieces of equipment together.
In the context of lathes, adapters are used to connect the lathe spindle to the chuck.
This is necessary because the chuck must be able to rotate at high speeds, and the lathe spindle is designed to rotate at slower speeds.
The adapter reduces speed, which makes it possible to use the chuck on the lathe.
There are two main types of adapters: threaded and tapered.
Threaded adapters have a series of threads that allow them to be screwed onto the lathe spindle.
Tapered adapters have a tapered surface that allows them to be slid onto the lathe spindle.
The type of adapter that is used will depend on the specific lathe and chuck that are being used.
So, these are the basics of the adapters that can be found in lathe machines.
Tool Rests
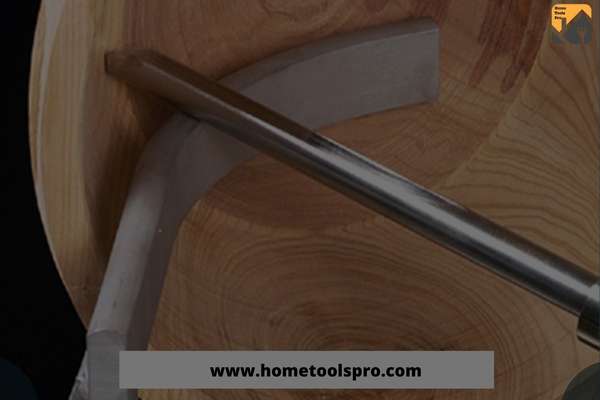
A tool rest is a device used to support and position a cutting tool on a lathe.
The tool rest allows the operator to safely and accurately position the cutting tool relative to the workpiece.
Several different types of tool rests are available, each designed for a specific type of lathe operation.
The most common type of tool rest is the fixed rest, which is attached to the lathe bed and cannot be moved.
Fixed rests are typically used for general-purpose machining operations such as turning, facing, and drilling.
Other types of tool rest include moveable rests, which can be positioned along the length of the lathe bed.
Its steady rests support the workpiece between centres and follow rests, which are used to support long unsupported workpieces.
Also, there are two types f tool rests based on their straight and curved shapes.
These different shapes are used to accommodate different shaped workpieces.
When choosing a tool rest, it is important to consider the type of lathe operation being performed and the size and weight of the cutting tool and workpiece.
A properly selected and positioned tool rest will help ensure safe, accurate, and efficient machining operations.
Tool Rest Set:
Measuring Tools

There are various measuring tools that can be used in order to work efficiently with a lathe machine. It is important to have a good understanding of how these tools work to use them properly.
Some are used to measure the external and internal diameters of objects. While some are, on the other hand, used to measure the thickness of objects.
It is important to choose the right tool for the job at hand. Each of these tools has its advantages and disadvantages. However, always try to go with the right measuring tool and minimise the precision.
So, some of the essential measuring tools of a lathe are as follows:
Divider:
A Divider Measuring Tool is a tool that helps to measure the distance between two points on a workpiece while it is being turned on a lathe.
This measurement is important for ensuring that the workpiece is machined evenly and with accuracy.
The divider measuring tool typically consists of two adjustable metal legs, allowing the user to set the distance between them as desired.
The tool is then placed against the workpiece at the desired points, and the distance between the legs is read off on a scale or ruler to get an accurate measurement.
Caliper:
A calliper is a measuring tool used to measure the diameter of an object. It has two parallel arms that open and close, allowing you to measure the thickness of something or the distance between two points.
In a lathe, a calliper is used as part of the process of machining parts. The calliper is inserted into a hole in the workpiece and then turned on its side. This causes it to pinch the workpiece and measure its diameter.
The information collected by the calliper can then be used to set up the machine’s cutting tools so that they remove precisely the right amount of material from the workpiece.
Clear Acrylic for Drawing Circles:
The Clear Acrylic for Drawing Circles Measuring Tool in Lathe is great for anyone who needs to measure circles and other shapes.
This tool is made of clear acrylic, so it is easy to see what you are measuring. It also has a built-in protractor, so you can easily measure angles.
This tool is great for measuring boards, pipes, and other objects that are round or have curved surfaces.
Steel Protractor:
A protractor is a measuring tool used to measure angles. The most common type of protractor is the steel protractor, which is used to measure angles in lathes.
The steel protractor consists of two arms that intersect at a point, with one arm having a scale marked in degrees and the other arm having a pointer.
To use the steel protractor, the aim point is placed on the vertex (the point at which the two arms intersect), and the angle is read off of the scale.
A steel protractor is an essential tool in lathe work, as it allows for precise measurement of angles.
When working with Lathes, it is important to be able to make accurate measurements, as even small inaccuracies can lead to big problems down the line.
Digital Protractor:
A digital protractor is a measuring tool used to help ensure accurate angles are being machined when working with metal on a lathe.
It does this by providing a numerical readout of the angle turned, which can then be compared against the desired angle to ensure accuracy.
This is especially important when machining parts that need to mate with other parts to create a finished product, as even small inaccuracies can lead to problems down the line.
Divider 3 in One:
Clear Acrylic:
Steel Protractor:
Maintenance Tools
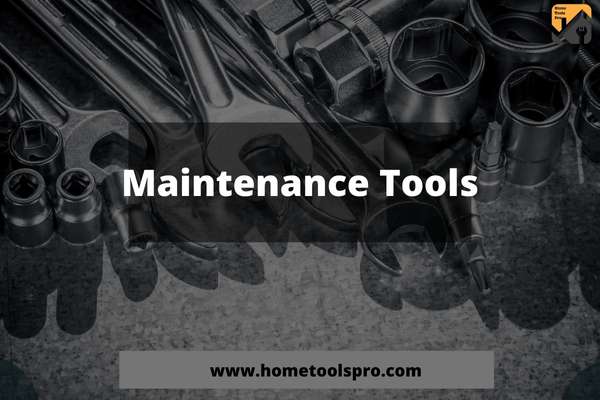
Maintenance tools are important for a lathe because they allow the lathe to be properly maintained and kept in good working order.
A lathe can become damaged and may not work properly without proper maintenance. Maintenance tools include wrenches, screwdrivers, and other tools used to tighten or loosen screws, bolts, and other parts on the lathe.
They also include tools used to clean the machine and remove debris or dust from its parts. Following are some of the most commonly used maintenance tools of a lathe machine.
Contact Cleaners:
Contact cleaners are important for maintaining lathes because they help keep the machine clean and free of debris.
This assists in the overall performance of the machine and helps to prolong its life. Contact cleaners can be found at most hardware stores and online retailers.
Grease Oil:
Regular maintenance of your lathe machine is important to keep it running smoothly and prevent potential problems.
Grease oil can help by lubricating the moving parts of the lathe, which can reduce wear and tear.
In addition, grease oil can help to keep the surface of the lathe clean and free from debris, which can clog up the moving parts and cause problems. A little bit of grease oil goes a long way in maintaining your lathe machine.
Metal Wax:
Metal wax is a lubricant applied to the metal parts of a lathe machine. It helps to keep the metal parts from wearing down and keeps them in good condition.
Additionally, metal wax helps to reduce friction between the metal surfaces, which allows them to move more smoothly and increases the lifespan of the machine.
Micro Fibre Towel:
Microfibre towels are great for machine maintenance because they’re soft, durable, and absorbent.
They can be used to clean all of the surfaces of the machine without scratching or damaging them.
Additionally, the microfibres help remove oils, dust, and other debris from the machinery, which helps keep it running smoothly.
Contact Cleaners:
Grease Oil:
Metal Wax:
Other Accessories
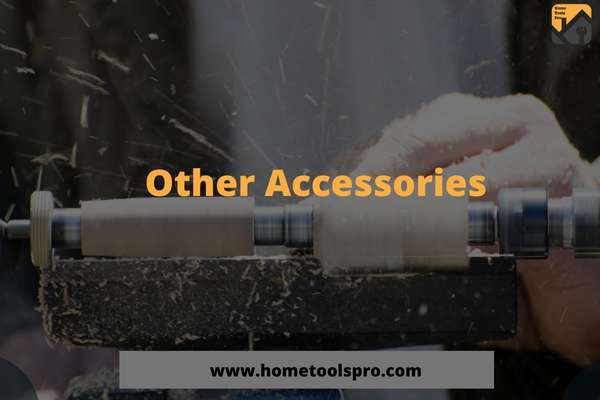
Lathe Light:
A lathe light is a must-have accessory for anyone who uses a lathe on a regular basis.
It provides essential illumination for tasks such as adding details to turned objects or cutting precise pieces of wood.
There are many different types of lathe lights available on the market, but they all serve the same purpose to provide a clear, bright light source that can be directed onto the workpiece.
Adjustable Table:
An adjustable lathe table is important for a number of reasons.
It allows you to accurately position your workpiece for machining, which results in more precise cuts and a higher quality finished product.
An adjustable lathe table also ensures that the cutting tool is always at the correct height relative to the workpiece, which helps to prevent wear and tear on both the tool and the workpiece.
Finally, an adjustable lathe table makes it easier to get into tight spaces when machining smaller parts, saving time and improving accuracy.
Machine Work Light:
Lathe Table:
Related Matters
What is a lathe faceplate used for?
A faceplate is a disc that attaches to the spindle on a lathe and has holes drilled in it to which workpieces can be attached.
This allows the turned workpiece to be held more securely and eliminates the need for a chuck.
Faceplates are also used as mounting surfaces for sanding discs, grinding wheels, and other attachments.
Do you need a chuck for a lathe?
A lathe is a powerful machine that is used to shape and manipulate different materials.
In order to use a lathe, you will need a chuck. A chuck is a device that holds the material in place while it is being shaped by the lathe.
There are different types of chucks available for use with a lathe.
The type of chuck you will need will depend on the material you are working with and the specific project you are working on.
For example, if you want to turn a piece of wood on the lathe, you would need to use a wooden scroll chuck.
You can also echck out the Can You Weld an AiCompressor Tank? here.
What are spindle adapters in a lathe?
Spindle adapters are used to secure the workpiece in the spindle of a lathe.
The adapter is a cylindrical piece of metal with a threaded hole on one end and a tapered hole on the other.
The threaded hole is used to secure the adapter to the spindle, and the tapered hole is used to secure the workpiece in place.
How do you use a spur drive centre in a lathe?
A spur drive centre is a lathe centre with a pointed spur on the end.
This type of centre is used to support short workpieces that would otherwise be too small to use a faceplate or chuck.
The point of the spur drives into the end of the workpiece, and the drive centre’s shaft rests against the side of the workpiece.
This provides stability and allows the workpiece to be turned.